Our Technology
\
Flow of Die Making
/
01
QUOTATION
QUOTATION & ORDER
Please feel free to contact us!
Please feel free to inquire about quotations and specifications.
We will cooperate with the relevant departments to make proposals that meet the needs of customers.
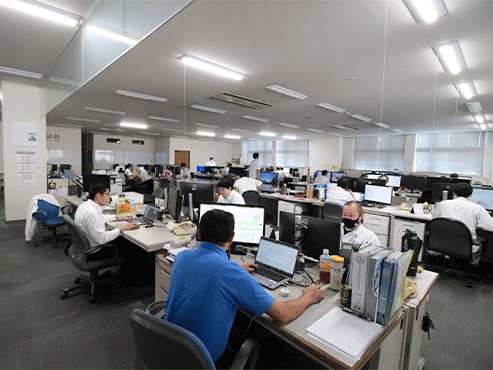
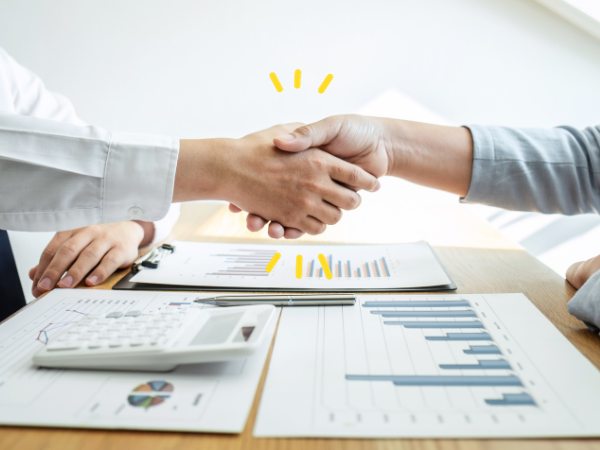
02
DESIGN
DIE DESIGN
Experienced engineers will offer you the best proposal to meet your needs!
SE
(Simultaneous Engineering)
We will help you from the early stages of your development. We find out problems and propose solutions both for feasibility verification using the latest software and process viability by experienced engineers. In addition, based on the production volume of the customer, it is possible to provide support such as proposing die specifications and selecting production facilities.
D/L (Die Layout)
The number of processes and the details of the process are determined based on the product data and equipment requirements received from customers. Even if the same product is designed differently, the number of processes and machining content will change. Therefore, we propose the most appropriate process settings based on the experience values.
3D design
Design dies for each process by reflecting the customer's die specifications and equipment requirements based on the process contents defined in the D/L.
We independently verify the selection of mold parts and the validity of the designed mold drawings, and use software to verify the strength and mass productivity of each area.
CAE (molding simulation)
The forming analysis is performed by Autoform on the analysis model created based on the process defined by D/L. A threshold value is defined based on our experience, and a forming method is determined based on the analysis results.
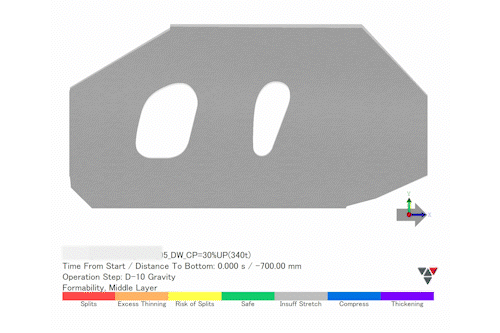
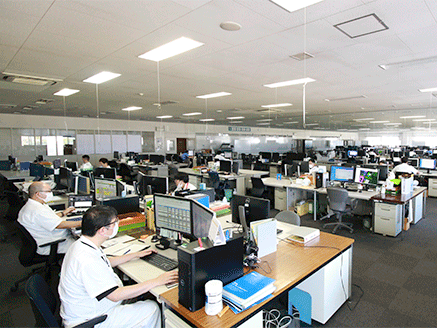
03
PRODUCTION
DIE PRODUCTION
Shorten lead time and improve quality with 24-hour machining and craftsmanship
Machining
Coordinated with NC Data Dept. to achieve automation by optimizing data settings based on various machining experience values and minimizing the intervention of machine operators to the limit. We are working to reduce lead time in die making by operating state-of-the-art machines around the clock.
Finishing/Press
With taking full advantage of the five senses of experienced craftsman, we can accommodate micron adjustments, which are difficult with machining technology. In recent years, we will integrate with simulation technology to further improve quality.
Utilize cutting-edge technologies
By proactively introducing cutting-edge technologies and reviewing depend on the person work that relies on human experience on a daily basis, we aim to create dies of more stable quality. We have introduced laser hardening machines to eliminate inconsistencies in manual hardening operations.
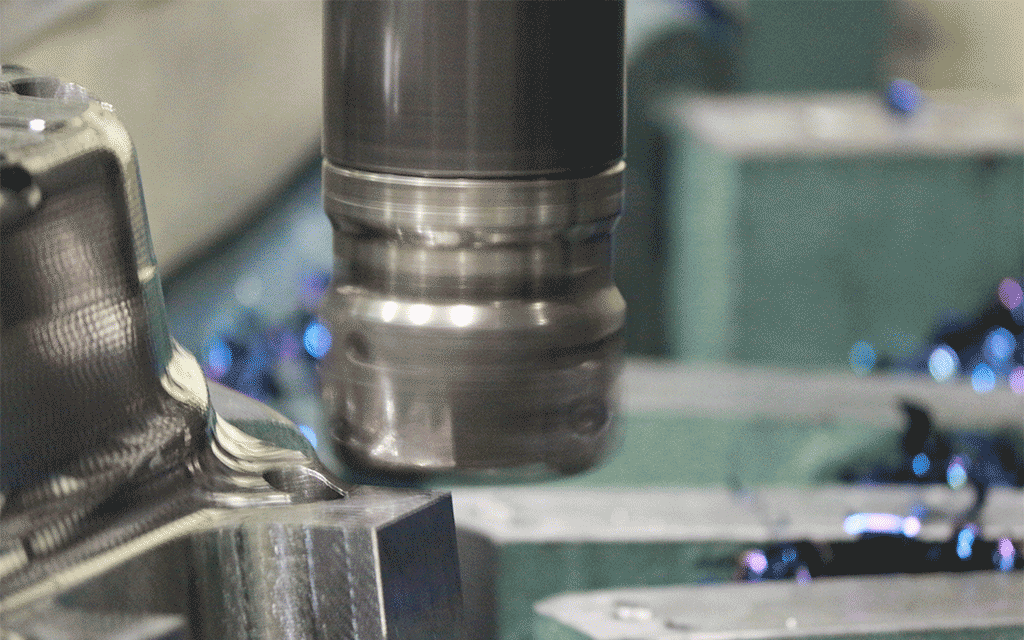
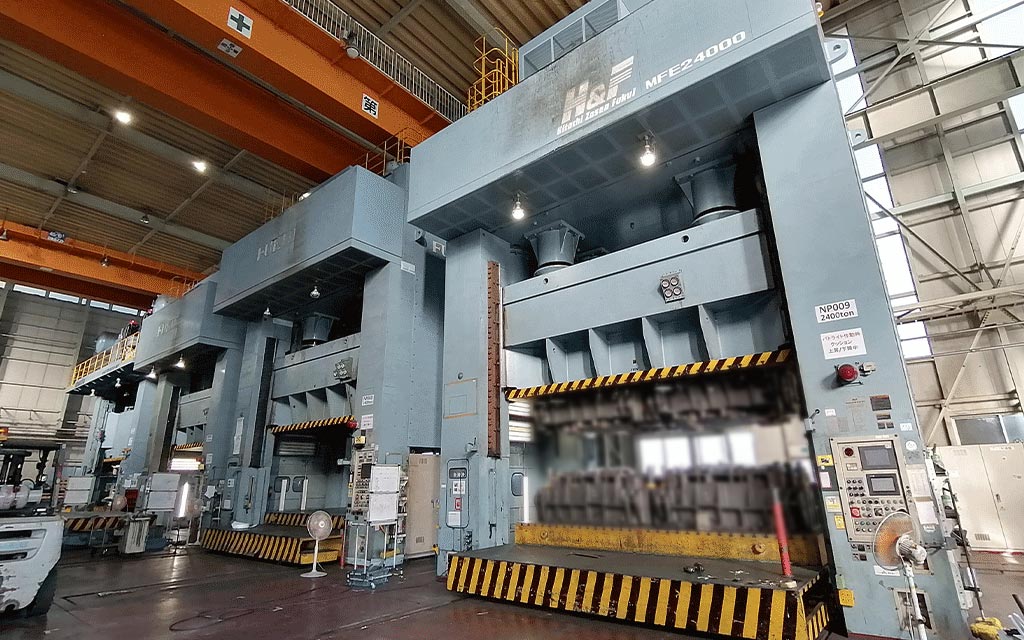
04
QUALITY
QUALITY ASSURANCE
Thorough inspections and quality assurance by a skilled inspector
Panel Quality Assurance
In addition to the contact type 3D measuring equipment, non-contact blue light 3D measuring equipment was installed at each factory, enabling more precise product quality checks. This is used to improve the quality of our products, mainly dies.
Quality assurance of dies
Experienced inspectors provide die quality assurance through independent inspections.
They have a deep understanding of customer specifications and is able to confirm if dies are produced according to customer's needs.
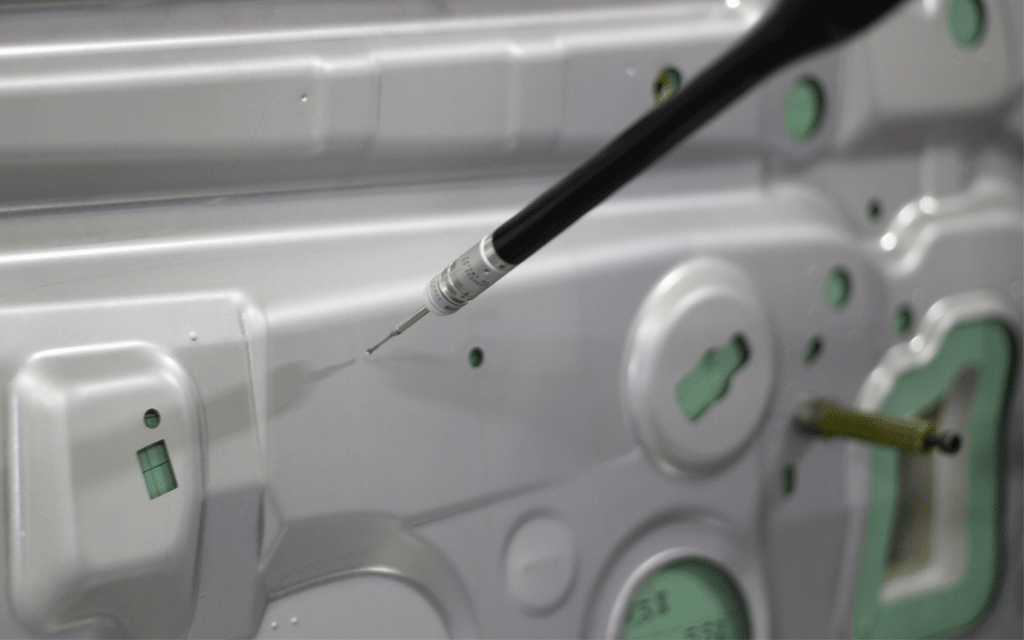
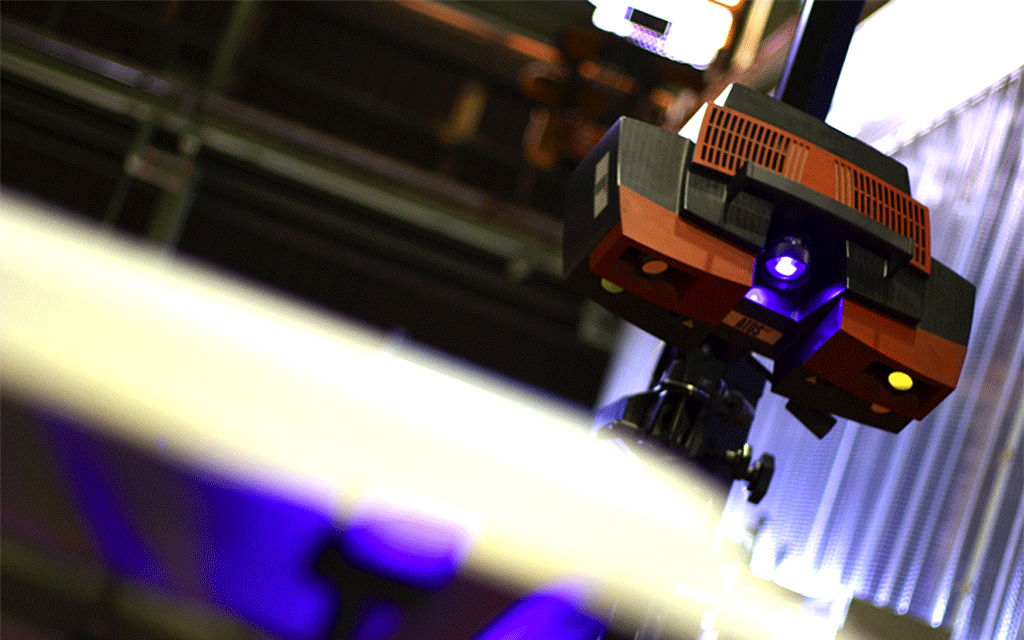
05
PJ MANAGEMENT
PROJECT MANAGEMENT
Total coordination from order to shipment
Project Manager System
We have introduced a project manager system as a series of contact points, from meetings held before and after receiving orders to delivery of dies to customers. We will fulfill our role of coordinating with customers to meet the needs of a wide variety of customers.
Group of professionals familiar with stamping dies
Bodypress technology specialists, who have handled difficult products such as Body Side and Fender, participate in the project from the stage of product analysis before design, and incorporate the know-how according to the features of the product into the processing data. We will also act as a bridge between the technology and manufacturing divisions in the quality loop process to improve quality from an early stage.
Production management system linking design and production
Based on the schedule of the customer, we have built our own production management system, which includes the phases of die design and die manufacturing. In particular, the machining schedule for each die with a large number of workpieces is managed on a piece-by-piece and hourly basis, and the system is operated in an integrated system that transcends departmental boundaries.
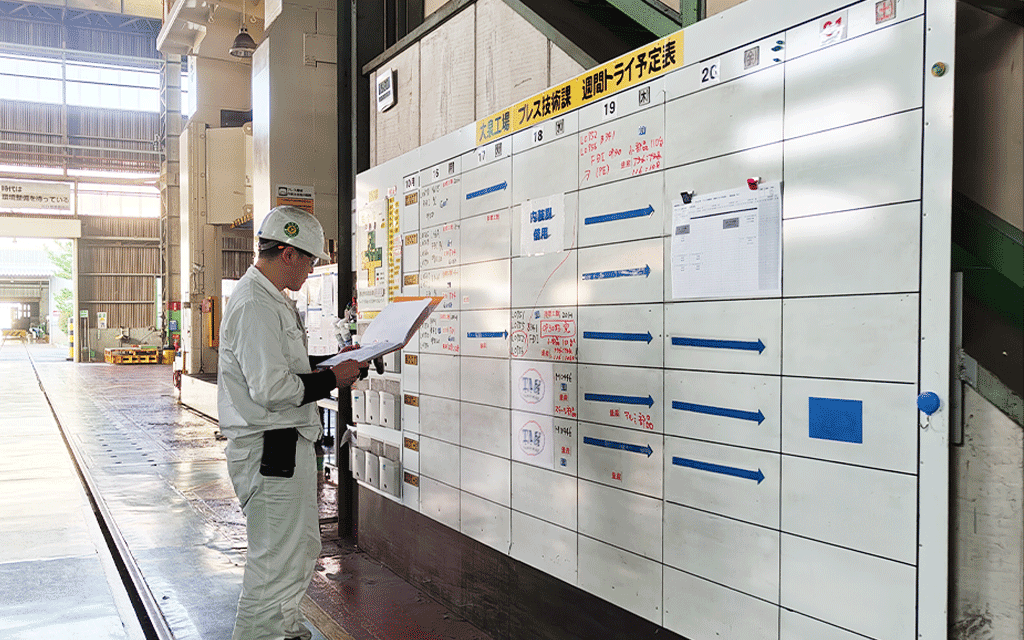
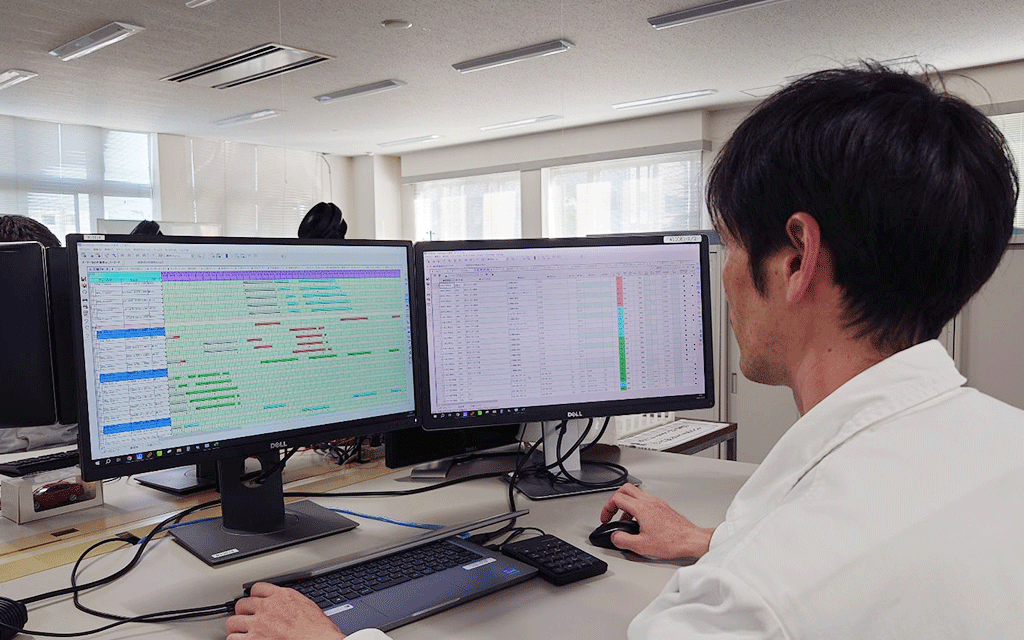
After service
On-site work/maintenance (SV)
Adjustment against to delivered dies is accommodated according to the equipment on the site.
Experience of dispatching engineers not only in Japan but also around the world.
It is also possible to solve problems during mass production and dispatch personnel to maintenance dies.
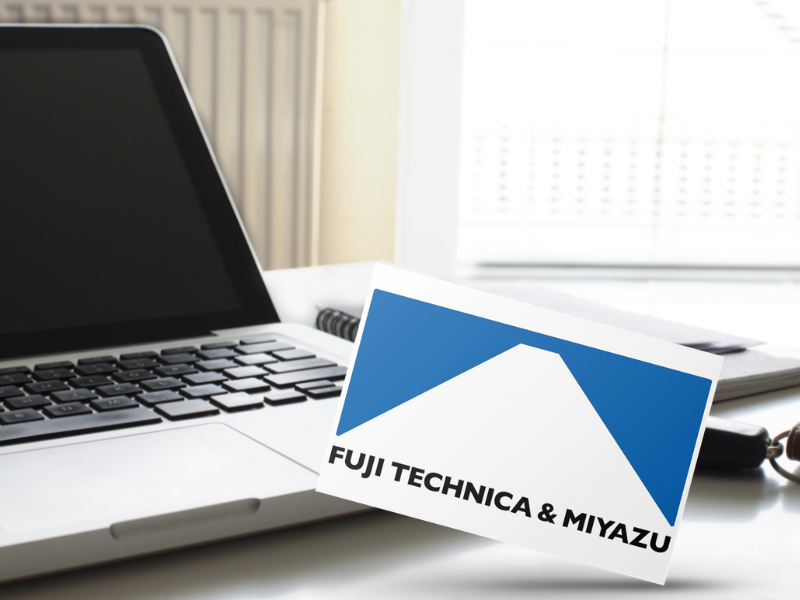
Contact
Please feel free to contact us for job inquiries and estimates.